Já está no ar a revista de Máquinas-ferramenta ROMI! Além de notícias e novidades, você pode encontrar informações sobre a nossa linha completa de equipamentos, composta por centros de usinagem, centros de torneamento, tornos universais, tornos CNC, mandrilhadora e centros de usinagem para manufatura híbrida, que combinam as operações de usinagem e manufatura aditiva (impressão 3D) em um único equipamento.
Um dos temas abordados é a reprodução da taça Jules Rimet com o processo de manufatura híbrida em um Centro de Usinagem ROMI D 800 Hybrid, uma ação conjunta da Romi com a EESC-USP, a FAPESP e a empresa Hybrid Manufacturing. Outro destaque são as tecnologias em usinagem, como o gear hobbing para a produção de engrenagens e o polygonal turning, que permite obter formas não circulares em peças fabricadas em centros de torneamento.
Nesta publicação você encontra links e QR Codes para acessar vídeos e conteúdos exclusivos. Para ver todas essas novidades, clique aqui e faça o download da revista.
Prepare-se para receber sua máquina Romi!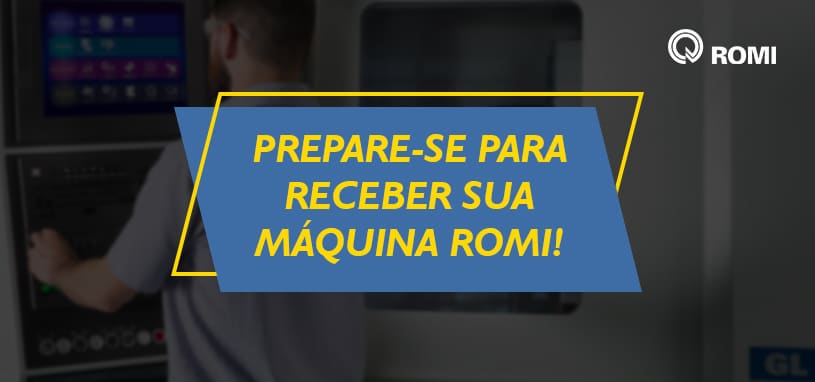
Definido o equipamento ideal para sua produção e negociado todos os termos de contrato, chegou a hora de receber seu novo equipamento e colocá-lo em operação. Para que o funcionamento inicial da sua máquina seja realizado de forma adequada, algumas ações devem ser executadas no local de instalação antes do recebimento. Confira o passo a passo das principais providências iniciais e esteja preparado para receber sua nova máquina Romi.
Planta da Fundação
O primeiro passo é preparar adequadamente a fundação do local em que a máquina será instalada, isso garante a correta ancoragem e isolamento de vibrações externas, prevenindo contra possíveis torções da estrutura da máquina por deslocamento ou acomodação do solo.
Fundações inadequadas podem causar diversos problemas na operação, como a alteração na geometria da máquina, aumento no consumo de energia, redução da vida útil de componentes, folgas e desgastes prematuros, vibrações durante a usinagem e erros dimensionais, geométricos e de rugosidade em peças acabadas.
Por isso, a máquina deve ser instalada em uma fundação firme e longe de fontes de vibração, caso não seja possível, um sulco antivibração deve ser colocado ao redor da fundação para garantir sua estabilidade, o local também deve ser seco e sem luz direta do sol.
A máquina deve estar nivelada e os parafusos de ancoragem devem ser travados uniformemente. É importante ressaltar que os chumbadores não podem estar fixados no piso antes do recebimento da máquina, pois isso fará com que a transportadora não posicione sua máquina no local correto, ficando a cargo do cliente a reconstrução da ancoragem.
Instalação Elétrica
O segundo passo é adequar as instalações elétricas, considerando que a máquina deve ser alimentada por uma rede nominal trifásica balanceada, seguindo a flutuação máxima de tensão e frequência nominal indicadas no Manual de Providências Iniciais, específico para cada equipamento.
É necessário prestar atenção ao comprimento do ramal, que se superior a 30 metros, o cabo deve ser redimensionado. Outro detalhe importante diz respeito ao aterramento, que deve ter resistência menor ou igual a cinco ohms, dimensionado de acordo com a potência instalada. Se houver mais de uma máquina, elas podem usar o mesmo aterramento, desde que, as ligações usem condutores de proteção independentes.
Além de consultar a regulamentação local para preparação do aterramento, o recomendado é contratar uma empresa especializada para realizar o serviço de dimensionamento e instalação do aterramento. Instalações incorretas podem danificar o equipamento e ocasionar a perda da garantia, caso o serviço não atenda a especificação do Manual de Providências Iniciais, fornecida no momento da aquisição do equipamento.
Instalação Pneumática
A instalação pneumática é o terceiro item que deve ser preparado antecipadamente, é recomendado a utilização de filtros e secadores para garantir a qualidade do ar fornecido pela rede pneumática. Neste processo, vários fatores devem ser avaliados, como a potência do compressor, tipo de compressor, umidade do ar, condições ambientais, entre outros. Por esse motivo, a contratação de um especialista neste processo é importantíssima para o bom funcionamento do equipamento.
Abastecimento
Por último, está o abastecimento dos insumos da máquina: lubrificantes e refrigerante de corte. Esses itens precisam ser adquiridos antes da chegada da máquina, possibilitando que no momento da instalação todos os testes de operação e funcionamento finais sejam executados.
Ao seguir o Manual de Providencias Iniciais, você garante que sua máquina Romi funcione corretamente e tenha um prolongado tempo de vida útil, permitindo o retorno completo do seu investimento. A Romi oferece o serviço de Entrega Técnica, fornecendo todas as informações sobre os recursos que a máquina e ajudando a sua empresa a alcançar o melhor desempenho nos equipamentos. Além disso, nossos equipamentos contam com garantia estendida, que podem variar conforme o modelo (consulte manual), assegurando mais confiabilidade e produtividade em suas máquinas por muito mais tempo.
Máquinas Locadas – ROMI MAAS
Para as máquinas locadas, além de todos os requisitos anteriores, é necessário disponibilizar um ponto de rede com Banda de internet dedicada de no mínimo de 2Mbps para até 10 máquinas instaladas, e a cada 10 máquinas adicionais é necessário acrescentar 1Mbps adicional. Para melhores resultados, recomenda-se banda de internet empresarial maior que 10 Mbps.
O ponto de rede é necessário para monitoramento e liberação remota do equipamento e deve estar preparado e ativo no momento da instalação da máquina.
Caso tenha qualquer dúvida sobre os procedimentos descritos no Manual de Providências iniciais ou precise de auxílio de nossos técnicos para instalação do seu equipamento, entre em contato com a RAI (Romi Assistência Integral), pelo telefone (19) 3455-9333 – opção 3 ou pelo e-mail posvenda@romi.com.
6 tecnologias que elevam sua máquina-ferramenta ao máximo da produtividade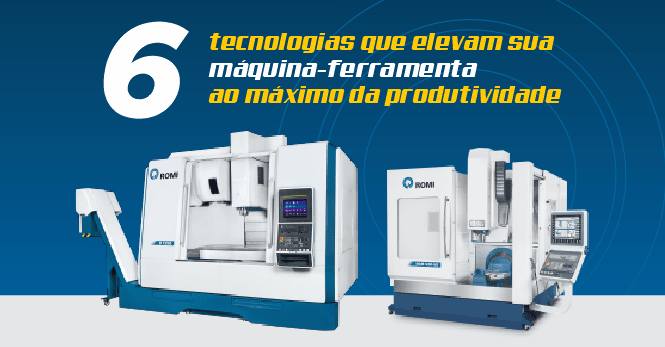
Nas últimas décadas, o surgimento de novas tecnologias causou uma verdadeira revolução no desenvolvimento dos projetos de máquinas-ferramenta. Com o passar dos anos, estes equipamentos, que antes limitavam-se em ser uma solução puramente mecânica para o arranque de cavacos, receberam controles digitais e componentes com alta tecnologia embarcada, e hoje fazem parte de células inteligentes de manufatura, comunicando-se com outros periféricos, como sistemas de carga e descarga automática de peças, tornando-se verdadeiros centros de operações.
Da concepção de uma estrutura robusta até a definição dos componentes eletrônicos, há muito mais do que imaginamos quando o assunto é tornar as máquinas-ferramenta capazes de operar com mais eficiência, mantendo, ao mesmo tempo, sua precisão. Destacamos abaixo algumas dessas tecnologias e componentes para entendermos como eles influenciam o funcionamento de um centro de usinagem, proporcionando uma operação ágil e eficiente:
1. Cabeçote Direct Drive
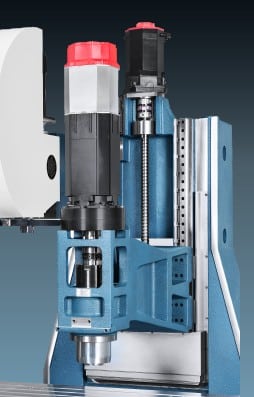
Considerado um dos componentes mais precisos de um Centro de Usinagem CNC, o cabeçote é a interface entre a ferramenta, que faz a retirada do material, desbaste ou acabamento das peças, e o motor principal da máquina.
Cabeçotes Direct Drive (com motor diretamente acoplado ao cabeçote), possuem altas taxas de aceleração, resultando em tempos de ciclos menores. Além disso, apresentam excelente precisão de giro mesmo em altas rotações. Os Cabeçotes Direct Drive, que equipam os Centros de Usinagem da nova geração da Linha ROMI D, proporcionam excelente acabamento, grande eficiência na transmissão, torque, potência e rotação, em versões até 15.000 rpm.
2. CNC
A partir da década de 60, computadores foram introduzidos nas máquinas-ferramenta, fato este que permitiu o desenvolvimento de equipamentos mais modernos. O advento do CNC fez com que as máquinas conseguissem repetir com maior precisão uma sequência de movimentos, o que aumentou a qualidade dos produtos, diminuiu o retrabalho e o desperdício e tornou as linhas de produção mais rápidas e flexíveis.
Graças à alta capacidade dos processadores e a evolução do código e da linguagem de máquina, hoje os CNCs processam programas muito mais rapidamente. Acompanhando o desenvolvimento da informática, a necessidade de conectividade e a tendência por uma interatividade cada vez maior com o usuário, novas funcionalidades também surgiram para facilitar a operação e proporcionar uma experiência homem-máquina cada vez mais amigável.
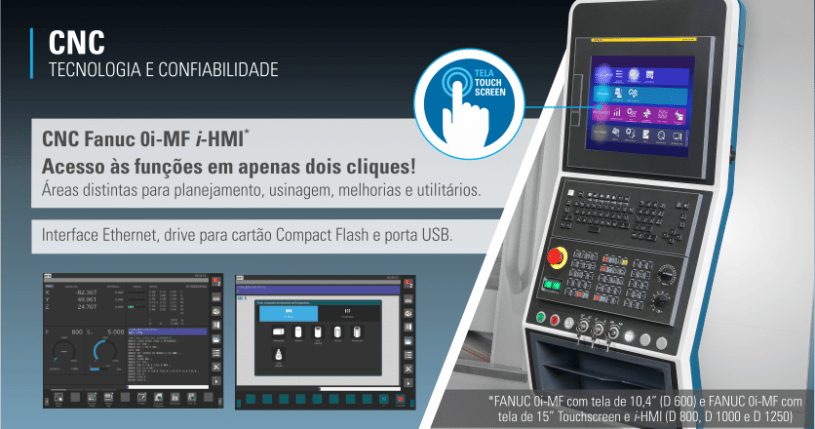
O CNC Fanuc 0i-MF i-HMI, utilizado nos modelos ROMI D 800, ROMI D 1000 e ROMI D 1250 em monitores touchscreen de 15”, oferece ao usuário grandes facilidades de programação, com tela principal com áreas distintas para planejamento, usinagem, melhorias e utilitários, permitindo acesso às funções favoritas em apenas dois cliques. Possui interface Ethernet, drive para cartão Compact Flash e porta USB. Algumas outras funcionalidades são:
- Ambiente que proporciona a visualização de várias informações em uma única tela;
- Gerenciador de ferramentas com possibilidade de inserção dos desenhos, facilitando sua identificação durante o setup;
- Recursos para manutenção corretiva e preventiva;
- Os programas de usinagem podem ser facilmente acessados e organizados em pastas, com visualização do desenho das peças;
- Visualização de arquivos em vários formatos;
- Vários ciclos de usinagem interativos.
3. Guias Lineares de Rolos
As guias lineares são elementos que permitem a um componente deslizar ao longo de outro, permitindo o movimento dentro de um padrão linear preciso, com a absorção de vibrações e altas taxas de avanço. Elementos fundamentais nas máquinas-ferramenta, devem ser rígidas o suficiente para não prejudicar a precisão geométrica ou dimensional do equipamento.
As Guias Lineares de Rolos, oferecem alta rigidez e menor deformação sob cargas flutuantes (variadas) repetidas, pois os rolos são posicionados em uma forma balanceada, permitindo receber cargas em todas as direções. Outros benefícios são:
– Melhoria na capacidade de corte e melhor desempenho no acabamento;
– Vida útil ampliada e movimentos suaves e silenciosos;
– Demandam baixo consumo de óleo lubrificante
– Área de contato maior se comparadas com as guias de esferas, obtendo-se maior capacidade de carga.
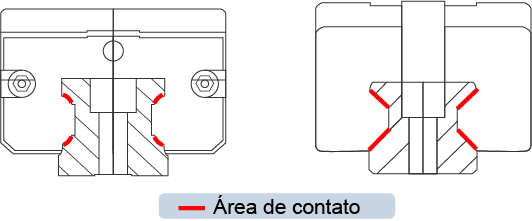
Guia linear de esferas X Guia linear de rolos
Na nova geração da Linha ROMI D e na Linha ROMI DCM 620, as Guias Lineares de Rolos permitem altas taxas de avanço e aceleração além de posicionamento rápido dos eixos, minimizando tempos passivos e aumentando a produtividade.
4. Sistema de Compensação Térmica
A estabilidade térmica é um dos requisitos fundamentais no projeto de uma máquina-ferramenta. Soluções para evitar desvios causados por variações térmicas tornaram-se cada vez mais imprescindíveis para obter-se maior precisão dimensional nos processos de usinagem.
No sistema de compensação térmica, através da coleta dos dados de temperatura dos sensores posicionados em locais estratégicos, o CNC faz a correção da posição real de cada eixo, fazendo com que a posição da ferramenta siga uma trajetória de maior precisão e possibilitando resultados dimensionais estáveis mesmo em longos períodos de trabalho.
Todos os modelos da Linha ROMI D – Nova Geração e da Linha ROMI DCM 620 possuem o sistema de compensação térmica, desenvolvido para reduzir os efeitos da oscilação de temperatura no dimensional das peças usinadas.
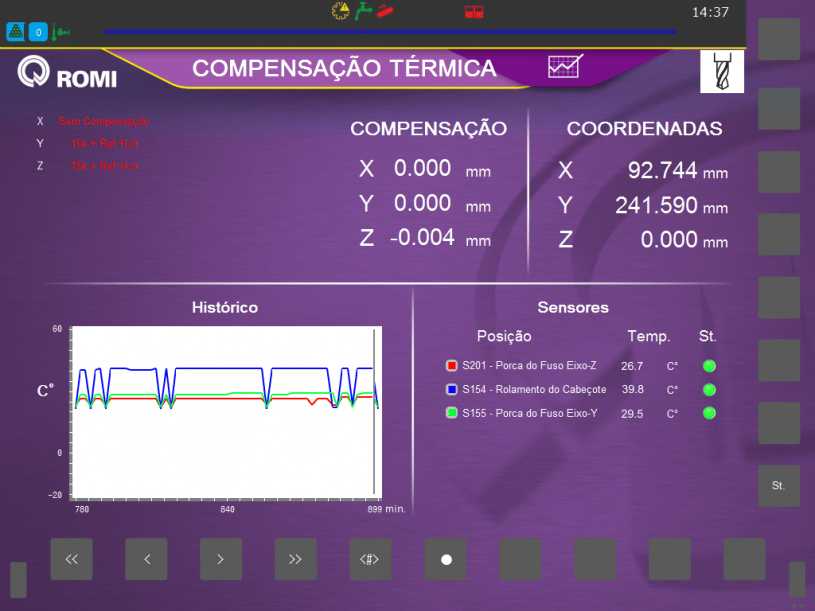
5. Correto dimensionamento dos componentes
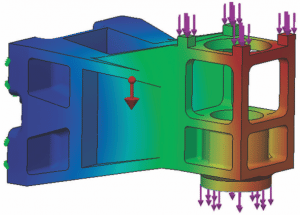
Quando falamos da estrutura de uma máquina-ferramenta, podemos destacar o componente principal: a base. Sobre a base, serão apoiados todos os demais componentes do equipamento e, portanto, ela deve ser capaz de resistir e amortecer os efeitos do tempo, devido a vibrações, variações de temperatura, carregamentos, movimentos e outros fatores. Outro componente estrutural é a coluna, que apoiada sobre a base, recebe o conjunto do cabeçote/spindle.
Atualmente dispomos de tecnologias que simulam situações reais de uso, permitindo adequações de projeto antes mesmo de ele sair do “papel”. Através do uso da análise de elementos finitos, por exemplo, é possível predizer como a estrutura irá comportar-se devido a sua construção e a disposição de seus componentes, possibilitando avaliar a melhor configuração no que diz respeito a rigidez e deformações. É importante que o modelo virtual da máquina compreenda as características reais como material, as condições de contorno e os movimentos, para que a análise apresente resultados confiáveis.
O dimensionamento correto de cada componente estrutural, é fator determinante para fazer com que uma máquina-ferramenta seja rígida e robusta. Estas características permitem maiores taxas de arranque de cavaco, como por exemplo neste vídeo do Centro de Usinagem ROMI D, usinando com uma profundidade de corte de 14mm:
6. Verificações geométricas e de performance
Antes de uma máquina-ferramenta ser entregue aos nosso clientes, realizamos verificações e testes para avaliar o desempenho do equipamento e sua adequação com os padrões estabelecidos. Um dos testes é o Ball Bar, com o qual verificamos o alinhamento dos eixos e asseguramos uma perfeita interpolação de movimento.
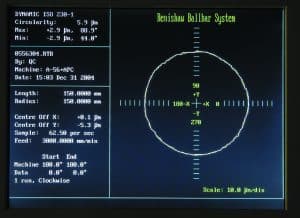
Todas as máquinas também são inspecionadas com sistema a laser para medição de posicionamento e repetibilidade.
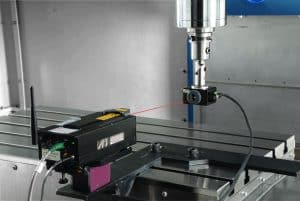
Além disso, realizamos o teste de funcionamento de 50 horas, no qual os equipamentos são submetidos a rotinas que simulam a sua utilização em situações extremas, e nos permitem avaliar, por exemplo, a estanqueidade (se há vazamentos), seu comportamento na movimentação dos eixos e rotações limites, além de trocas de ferramentas.
Saiba como aumentar a sua produtividade na usinagemAo pensar na evolução dos processos de usinagem convencionais, antes suportados apenas por tornos mecânicos, fresadoras ou furadeiras, atualmente nos deparamos com tornos CNC, centros de torneamento e centros de usinagem modernos, que possibilitam a usinagem de peças por completo, e até mesmo em uma única fixação, como por exemplo o Centro de Usinagem Vertical ROMI DCM 620-5X.
Seja qual for o tamanho do seu negócio, impulsionar a produtividade na usinagem é fundamental para manter a sua competitividade. Além da transformação tecnológica proporcionada pela renovação do parque de máquinas, é possível obter resultados significativos adotando boas práticas, com foco também nas pessoas e nos processos. Veja a seguir algumas dicas que vão ajudá-lo a desenhar processos de usinagem mais produtivos para o seu negócio:
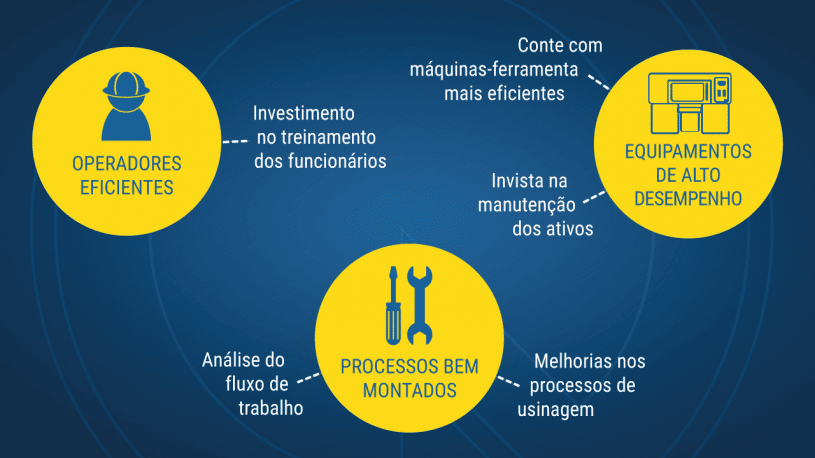
1. Faça uma análise do fluxo de trabalho existente
Uma boa maneira de aumentar a produtividade na usinagem é identificar pontos do fluxo de trabalho que precisam de atenção. Para isso, é preciso mapear visualmente todas as etapas necessárias para a fabricação de seus produtos, entendendo quais são as entradas e saídas de cada processo, os procedimentos, recursos necessários, responsabilidades, tempo de execução e métricas.
Considere criar fluxos detalhados para o monitoramento de cada processo. Assim, ficará mais fácil identificar as áreas com potenciais de melhorias, falhas, atrasos, gargalos ou problemas de capacidade, sendo possível desenvolver soluções e melhorias.
2. Invista no treinamento dos funcionários
A indústria de manufatura, máquinas-ferramenta e ferramentas de corte está em constante evolução, criando e implementando novas tecnologias para deixar os equipamentos mais robustos e, assim, proporcionar mais agilidade à produção. Diante deste cenário, é comum que os funcionários tenham de desenvolver e aprimorar diferentes habilidades para executar determinadas tarefas.
Por isso, é importante contar com um programa de treinamento contínuo para garantir que seus funcionários estejam tirando o máximo proveito das capacidades das máquinas-ferramenta e seus periféricos. Quando devidamente treinados, os funcionários trabalham motivados e de maneira otimizada, buscando sempre entregar melhores resultados.
3. Estude melhorias para os processos de usinagem
Para atender as expectativas e exigências de um cliente de itens usinados, o desenvolvimento de um processo de fabricação adequado, produtivo e econômico é indispensável. Cada item a ser fabricado possui particularidades que tornam seu processo produtivo único, seja por sua complexidade construtiva, material ou acabamento.
Estudos detalhados de usinagem, considerando todos os aspectos da peça a ser desenvolvida – e aqui falamos de itens como os parâmetros, ferramentas e condições de corte – permitem analisar as variáveis do processo e buscar soluções adequadas para obter os melhores resultados. Salientamos também, que em um processo de usinagem, assim como qualquer outro processo, devemos buscar a melhoria contínua, introduzindo novas tecnologias ou possibilidades.
4. Conte com máquinas-ferramenta mais inteligentes
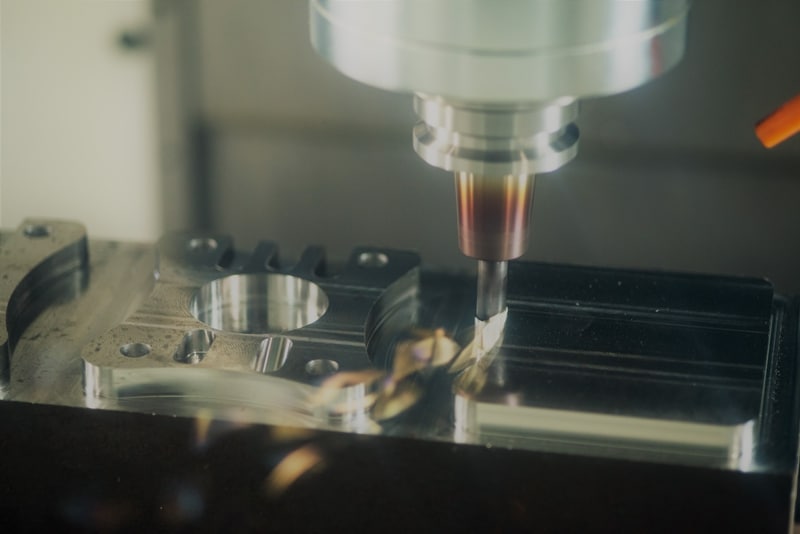
A evolução das máquinas-ferramenta é um dos itens que mais impactam quando pensamos em tornar a usinagem mais eficiente e flexível. Atualmente, por meio da informatização, controles digitais, equipamentos e sistemas de desenvolvimento de produtos e controles de produção, estes equipamentos funcionam como verdadeiros centros de operações.
Contar com tornos CNC, centros de usinagem, centros de torneamento e outras ferramentas com alto nível de robustez e precisão, é fundamental para garantir mais produtividade na usinagem. Diante deste cenário, hoje é possível produzir muito mais, mesmo diante de necessidades de produção complexas, reduzindo custos e aumentando a precisão e a qualidade da produção.
A capacidade de integração das máquinas-ferramenta também está contribuindo para a criação de processos de usinagem muito mais inteligentes e automatizados. Um exemplo são os Centros de Usinagem Verticais da Linha ROMI D – Nova Geração. Todos os modelos da Linha ROMI D possuem o sistema de compensação térmica, desenvolvido para reduzir os efeitos da oscilação de temperatura no dimensional das peças usinadas.
Através da coleta dos dados de temperatura dos sensores posicionados em locais estratégicos, o CNC faz a correção da posição real de cada eixo, fazendo com que a posição da ferramenta siga uma trajetória de maior precisão e possibilitando resultados dimensionais estáveis mesmo em longos períodos de trabalho.
5. Invista na manutenção dos ativos
Uma boa gestão de manutenção tem um impacto considerável nos custos associados com máquinas paradas, bem como no tempo e no orçamento investido em correções. Para isso, é fundamental criar uma rotina de manutenção dos ativos, que seja adequada à programação produtiva da empresa, considerando inspeções de rotina e agendando manutenções preventivas, pois novos equipamentos podem impulsionar a produtividade, mas também é preciso garantir sua longevidade e seu correto funcionamento.
Confira em nosso site, na área de peças e serviços, nossas dicas de manutenção para máquinas-ferramenta Romi. Aproveite também nossa promoção de 25% de desconto na mão de obra e em peças utilizadas nos serviços de revisão preventiva agendados até 30/11/2018 e concluídos até 31/12/2018.