6 tecnologias que elevam sua máquina-ferramenta ao máximo da produtividade
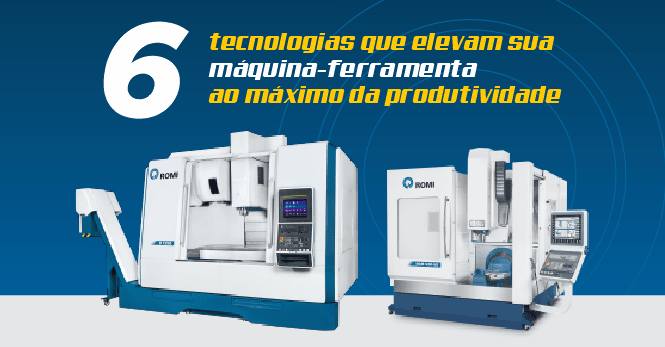
Nas últimas décadas, o surgimento de novas tecnologias causou uma verdadeira revolução no desenvolvimento dos projetos de máquinas-ferramenta. Com o passar dos anos, estes equipamentos, que antes limitavam-se em ser uma solução puramente mecânica para o arranque de cavacos, receberam controles digitais e componentes com alta tecnologia embarcada, e hoje fazem parte de células inteligentes de manufatura, comunicando-se com outros periféricos, como sistemas de carga e descarga automática de peças, tornando-se verdadeiros centros de operações.
Da concepção de uma estrutura robusta até a definição dos componentes eletrônicos, há muito mais do que imaginamos quando o assunto é tornar as máquinas-ferramenta capazes de operar com mais eficiência, mantendo, ao mesmo tempo, sua precisão. Destacamos abaixo algumas dessas tecnologias e componentes para entendermos como eles influenciam o funcionamento de um centro de usinagem, proporcionando uma operação ágil e eficiente:
1. Cabeçote Direct Drive
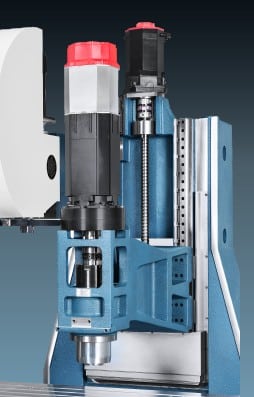
Considerado um dos componentes mais precisos de um Centro de Usinagem CNC, o cabeçote é a interface entre a ferramenta, que faz a retirada do material, desbaste ou acabamento das peças, e o motor principal da máquina.
Cabeçotes Direct Drive (com motor diretamente acoplado ao cabeçote), possuem altas taxas de aceleração, resultando em tempos de ciclos menores. Além disso, apresentam excelente precisão de giro mesmo em altas rotações. Os Cabeçotes Direct Drive, que equipam os Centros de Usinagem da nova geração da Linha ROMI D, proporcionam excelente acabamento, grande eficiência na transmissão, torque, potência e rotação, em versões até 15.000 rpm.
2. CNC
A partir da década de 60, computadores foram introduzidos nas máquinas-ferramenta, fato este que permitiu o desenvolvimento de equipamentos mais modernos. O advento do CNC fez com que as máquinas conseguissem repetir com maior precisão uma sequência de movimentos, o que aumentou a qualidade dos produtos, diminuiu o retrabalho e o desperdício e tornou as linhas de produção mais rápidas e flexíveis.
Graças à alta capacidade dos processadores e a evolução do código e da linguagem de máquina, hoje os CNCs processam programas muito mais rapidamente. Acompanhando o desenvolvimento da informática, a necessidade de conectividade e a tendência por uma interatividade cada vez maior com o usuário, novas funcionalidades também surgiram para facilitar a operação e proporcionar uma experiência homem-máquina cada vez mais amigável.
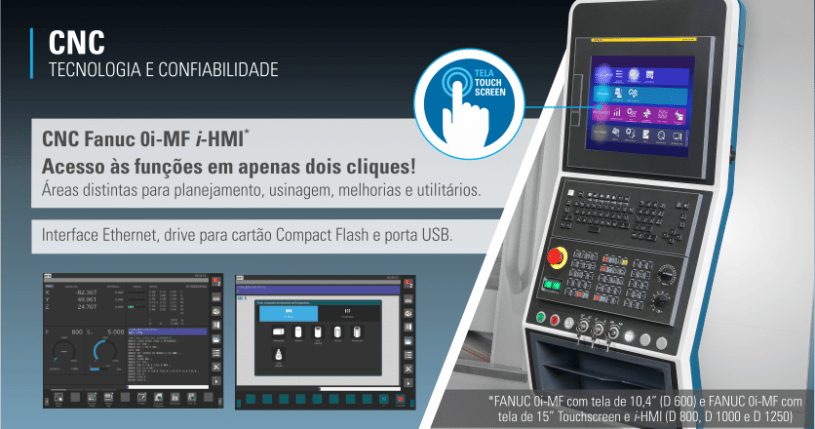
O CNC Fanuc 0i-MF i-HMI, utilizado nos modelos ROMI D 800, ROMI D 1000 e ROMI D 1250 em monitores touchscreen de 15”, oferece ao usuário grandes facilidades de programação, com tela principal com áreas distintas para planejamento, usinagem, melhorias e utilitários, permitindo acesso às funções favoritas em apenas dois cliques. Possui interface Ethernet, drive para cartão Compact Flash e porta USB. Algumas outras funcionalidades são:
- Ambiente que proporciona a visualização de várias informações em uma única tela;
- Gerenciador de ferramentas com possibilidade de inserção dos desenhos, facilitando sua identificação durante o setup;
- Recursos para manutenção corretiva e preventiva;
- Os programas de usinagem podem ser facilmente acessados e organizados em pastas, com visualização do desenho das peças;
- Visualização de arquivos em vários formatos;
- Vários ciclos de usinagem interativos.
3. Guias Lineares de Rolos
As guias lineares são elementos que permitem a um componente deslizar ao longo de outro, permitindo o movimento dentro de um padrão linear preciso, com a absorção de vibrações e altas taxas de avanço. Elementos fundamentais nas máquinas-ferramenta, devem ser rígidas o suficiente para não prejudicar a precisão geométrica ou dimensional do equipamento.
As Guias Lineares de Rolos, oferecem alta rigidez e menor deformação sob cargas flutuantes (variadas) repetidas, pois os rolos são posicionados em uma forma balanceada, permitindo receber cargas em todas as direções. Outros benefícios são:
– Melhoria na capacidade de corte e melhor desempenho no acabamento;
– Vida útil ampliada e movimentos suaves e silenciosos;
– Demandam baixo consumo de óleo lubrificante
– Área de contato maior se comparadas com as guias de esferas, obtendo-se maior capacidade de carga.
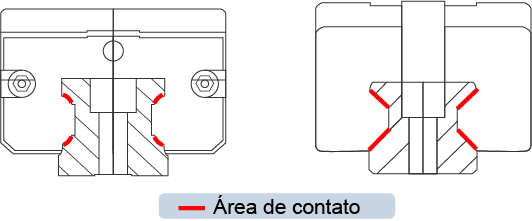
Guia linear de esferas X Guia linear de rolos
Na nova geração da Linha ROMI D e na Linha ROMI DCM 620, as Guias Lineares de Rolos permitem altas taxas de avanço e aceleração além de posicionamento rápido dos eixos, minimizando tempos passivos e aumentando a produtividade.
4. Sistema de Compensação Térmica
A estabilidade térmica é um dos requisitos fundamentais no projeto de uma máquina-ferramenta. Soluções para evitar desvios causados por variações térmicas tornaram-se cada vez mais imprescindíveis para obter-se maior precisão dimensional nos processos de usinagem.
No sistema de compensação térmica, através da coleta dos dados de temperatura dos sensores posicionados em locais estratégicos, o CNC faz a correção da posição real de cada eixo, fazendo com que a posição da ferramenta siga uma trajetória de maior precisão e possibilitando resultados dimensionais estáveis mesmo em longos períodos de trabalho.
Todos os modelos da Linha ROMI D – Nova Geração e da Linha ROMI DCM 620 possuem o sistema de compensação térmica, desenvolvido para reduzir os efeitos da oscilação de temperatura no dimensional das peças usinadas.
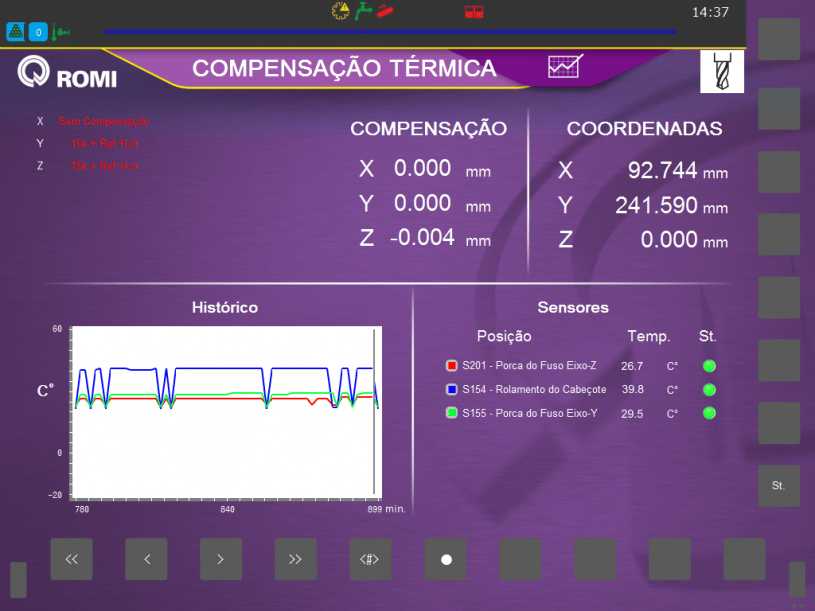
5. Correto dimensionamento dos componentes
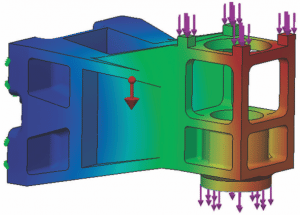
Quando falamos da estrutura de uma máquina-ferramenta, podemos destacar o componente principal: a base. Sobre a base, serão apoiados todos os demais componentes do equipamento e, portanto, ela deve ser capaz de resistir e amortecer os efeitos do tempo, devido a vibrações, variações de temperatura, carregamentos, movimentos e outros fatores. Outro componente estrutural é a coluna, que apoiada sobre a base, recebe o conjunto do cabeçote/spindle.
Atualmente dispomos de tecnologias que simulam situações reais de uso, permitindo adequações de projeto antes mesmo de ele sair do “papel”. Através do uso da análise de elementos finitos, por exemplo, é possível predizer como a estrutura irá comportar-se devido a sua construção e a disposição de seus componentes, possibilitando avaliar a melhor configuração no que diz respeito a rigidez e deformações. É importante que o modelo virtual da máquina compreenda as características reais como material, as condições de contorno e os movimentos, para que a análise apresente resultados confiáveis.
O dimensionamento correto de cada componente estrutural, é fator determinante para fazer com que uma máquina-ferramenta seja rígida e robusta. Estas características permitem maiores taxas de arranque de cavaco, como por exemplo neste vídeo do Centro de Usinagem ROMI D, usinando com uma profundidade de corte de 14mm:
6. Verificações geométricas e de performance
Antes de uma máquina-ferramenta ser entregue aos nosso clientes, realizamos verificações e testes para avaliar o desempenho do equipamento e sua adequação com os padrões estabelecidos. Um dos testes é o Ball Bar, com o qual verificamos o alinhamento dos eixos e asseguramos uma perfeita interpolação de movimento.
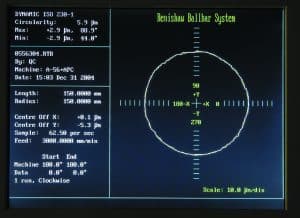
Todas as máquinas também são inspecionadas com sistema a laser para medição de posicionamento e repetibilidade.
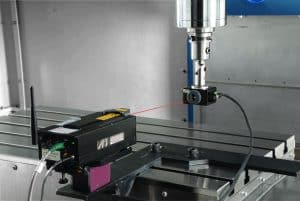
Além disso, realizamos o teste de funcionamento de 50 horas, no qual os equipamentos são submetidos a rotinas que simulam a sua utilização em situações extremas, e nos permitem avaliar, por exemplo, a estanqueidade (se há vazamentos), seu comportamento na movimentação dos eixos e rotações limites, além de trocas de ferramentas.